Comprehensive Packaging Equipment Service Solutions for Makers
Comprehensive Packaging Equipment Service Solutions for Makers
Blog Article
Specialist Product Packaging Equipment Solution for Seamless Procedures
In today's hectic manufacturing settings, the relevance of expert product packaging devices service can not be understated. Such solutions not only improve functional performance however additionally play an essential duty in minimizing downtime and making sure item top quality. By leveraging skilled professionals for precautionary maintenance and prompt repairs, businesses can navigate the intricacies of machinery administration (packaging equipment service). The landscape of tools service is developing, presenting both challenges and opportunities that necessitate additional expedition. What elements should companies consider when buying these vital solutions to protect their affordable edge?
Significance of Professional Solution

Furthermore, regular servicing by experts aids lengthen the life expectancy of product packaging tools. Expert service carriers are outfitted with thorough understanding of numerous machinery types and sector criteria, allowing them to carry out preventative upkeep effectively. This proactive strategy not only reduces the possibility of unexpected failures yet likewise improves total operational dependability.
Additionally, professional service can significantly contribute to compliance with governing standards. Packaging tools need to stick to stringent safety and security and high quality standards, and specialist specialists make certain that these requirements are fulfilled continually. This not just safeguards product integrity however additionally safeguards the company's reputation.
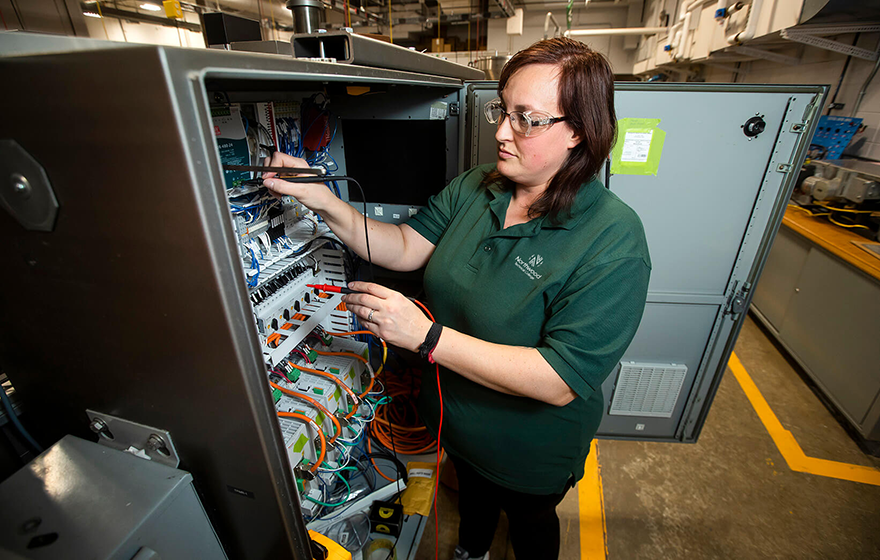
Advantages of Specialist Support
Engaging professional support for product packaging devices not just improves functional effectiveness yet additionally delivers a series of fringe benefits that can substantially impact a service's lower line. One of the most noteworthy advantages is the minimization of downtime. Specialist professionals can promptly detect and solve concerns, making sure that assembly line continue to be energetic and reducing the monetary losses related to idle machinery.
In addition, expert assistance typically includes preventative upkeep, which can expand the life-span of product packaging equipment. By consistently servicing machinery, prospective troubles can be recognized and resolved prior to they rise into expensive fixings or replacements. This proactive method not just saves money yet additionally boosts item high quality by making sure that devices runs within optimal criteria.
Furthermore, leveraging the proficiency of skilled experts can bring about improved conformity with industry policies. These professionals stay upgraded on the most recent criteria and can direct companies in carrying out best techniques, thus avoiding possible lawful obligations.
Kinds Of Product Packaging Equipment Services
When it comes to packaging devices services, organizations can pick from a range of options customized to fulfill their details demands. These services normally come under numerous groups, each made to boost operational effectiveness and reduce downtime.
Preventative upkeep solutions focus on normal evaluations and upkeep tasks to ensure that tools operates efficiently and decreases the likelihood of unanticipated failures. This proactive strategy can prolong the life expectancy of machinery and improve productivity.
Repair services are vital for addressing equipment malfunctions or failings - packaging equipment service. Experienced technicians diagnose the issues and do essential fixings, ensuring that the equipment is recovered to ideal working problems immediately
Installation solutions are critical when presenting new product packaging devices. Specialists take care of the setup, ensuring that More Bonuses the machinery is incorporated appropriately right into existing lines and functions as planned.
Training solutions offer personnel with the needed skills and understanding to run devices efficiently. This training can cover whatever from basic operation to advanced troubleshooting.
Finally, speaking with solutions offer strategic insights right into maximizing packaging processes, aiding businesses recognize locations for enhancement and execute ideal practices. Generally, selecting the best mix of these services can significantly improve packaging operations.
Secret Features to Try To Find
What vital features more helpful hints should businesses think about when picking packaging equipment solutions? Competence and experience are important. Suppliers with a tried and tested track document in the market can supply invaluable understandings and options tailored to certain functional needs. Additionally, the availability of extensive assistance services, including setup, upkeep, and troubleshooting, makes sure that services can depend on timely assistance when problems arise.
An additional trick feature is the versatility of service offerings. A company that can adapt to evolving organization demands, such as adjustments in manufacturing quantity or packaging requirements, will certainly contribute in maintaining performance. Innovation assimilation should be a priority; modern product packaging tools solutions should integrate advanced technologies, such as automation and real-time monitoring, to improve efficiency.
Last but not least, credibility and consumer comments must not be overlooked. Engaging with reviews and study can provide a clearer image of a solution provider's reliability and quality. By considering these important features, businesses can make informed decisions that will certainly sustain their product packaging procedures and add to general success.
Buying Long-Term Success
Buying long-term success in product packaging devices solutions needs a strategic approach that prioritizes sustainability and scalability. Companies must focus on selecting equipment that not just fulfills existing functional demands yet additionally accommodates future development and technical innovations. This insight lessens interruptions and boosts overall efficiency.
A vital element of this investment is the regular upkeep and service of equipment. Developing an aggressive solution schedule reduces downtime and expands the life expectancy of equipment, inevitably leading to set you back savings. Partnering with skilled service carriers makes certain that the tools is enhanced for efficiency, thus maintaining high production criteria.
Additionally, incorporating innovative innovations, such as automation and IoT article connectivity, can significantly improve functional capabilities. These innovations enable real-time monitoring and information evaluation, enabling business to make educated decisions that align with their long-term objectives.
Lastly, buying worker training on brand-new technology and best practices fosters a culture of constant improvement. By growing a competent workforce, companies can adjust to transforming market needs and keep their one-upmanship. Inevitably, a holistic method that includes tools, service, technology, and labor force development settings business for continual success in the product packaging sector.
Final Thought
In final thought, specialist product packaging devices service plays a crucial role in guaranteeing smooth procedures within production atmospheres. By prioritizing these solutions, organizations can attain optimum functional effectiveness and prolong the life expectancy of their equipment.
Report this page